Polyurethane foam (PU foam) is a versatile chemical product used in many common construction applications which require bonding, filling, sealing, and insulation. Its high thermal and acoustic insulation properties makes it an excellent product for applications such as insulation of waterpipes, bonding and sealing of roofs and walls and most important the installation of door and window frames.
Post your Requirement
The initial steps in Polyurethane chemistry started more than 80 years ago. Single component foams however were invented only in 1969 by ICI. During the 1970’s development of the product continued and since the early 1980’s PU foams have established for themselves an important place in the building industry and later in the DIY (Do-It-Yourself) market.Nowadays in most developed countries it is inconceivable to find a building site where no PU foam is used.
In India PU foams for building & construction applications were introduced hardly a decade ago and are unfortunately still not very popular in many different applications or projects. The slow implementation of this product can be explained by the fact that PU foam requires changes in building techniques/methods which is a process that takes some time. Also little product awareness and required applicator training for unskilled labour are the challenges for the growth of this product in building construction applications.
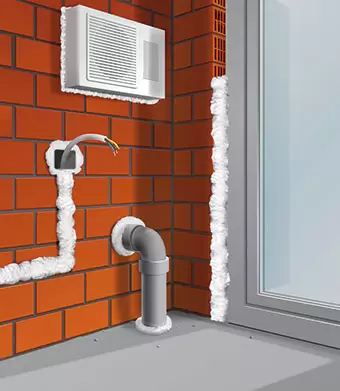
Soudal is the world leader in PU foams, having more than 30 years of experience producing, selling, and using PU foams all over the world. With four modern PU foam production plants in Belgium, Poland, Slovenia and China, Soudal manufactures over 90 million cans of PU foam a year. In India and other SAARC nations, the PU foam products under the global brand Soudafoam are distributed through the JV company McCoy Soudal Sealants, Adhesives & Foam Pvt. Ltd. based in New Delhi. McCoy Soudal is the market leader in PU foams in India and has trained over the past four years thousands of applicators in it McAademy training institute.
Characteristics of PU foam
- Forms a semi-rigid structure with more than 70% closed cells
- Excellent adhesion to most common building materials
- Can be trimmed, sanded and painted after full cure
- Large filling capacities
- Good thermal & acoustic insulation properties (table 1): soundproofing – filling air leakage
- Electric insulator
- Very easy to apply
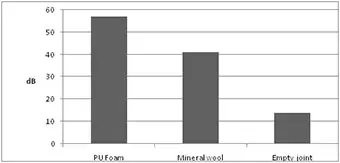
Application of windows with PU foam
In the window industry everyone talks about the quality of the profile, the type of glass and the other accessories like hardware etc. to fabricate a good quality system window having all the required features on insulation, aesthetics, durability, light transmission etc. All these elements have of course a crucial role to obtain all these features.
What is often neglected or not taken seriously is the installation part. You can have a window with the best, latest, state-of-the-art materials but if that window is not installed properly you will lose a lot of the insulation (acoustic & thermal) values through the joint/perimeter of the window and/or have leakages which will spoil the aesthetics around your window.
Therefore the use of quality sealants and PU foams plays a crucial role in obtaining a perfectly installed, waterproof and insulated window.
PU foam is generally used to fill the entire joint between the wall and the frame; it increases the insulation properties of the building and avoids “bridge” in which heat/cold or sound can be transferred freely.
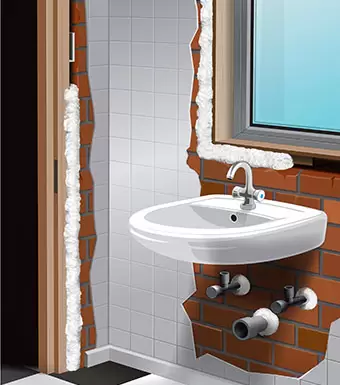
Sealants are applied over the PU foam to make the window weather/waterproof and protect the PU foam from UV.
Windows always first need to be attached mechanically, and strongly supported with all fittings in place (including spacers). Only using PU foam to fix a window is not sufficient for high wind load pressures.
Application steps of PU foam:
- Cans should be used in their recommended operating temperature as specified on the can. If the environmental temperature is too high or too low, keep foam cans at the optimal temperature for some time.
- Wear gloves, goggles, and other protective equipment.
- Ensure that the substrate is free of dust, grease and oil.
- It is almost always recommended to spray mists of water into the joint to promote adhesion and a faster curing rate.
- Shake the foam can well, for at least 30 seconds. The more, the better.
- For gun foams, fix the gun onto the can. For straw foams, fixed the provided straw onto the can.
- The can should be turned upside down for foaming.
- Extrude the foam into the joint from bottom-to-top, making sure the foam occupies 30-50% (straw foams) or 70-80% (guns foams) of the joint space, allowing space for expansion. There should not be holes or voids in the joint without foam, as this will compromise insulation.
- For best results, water can be sprayed into the joint, onto the foam, so that it cures faster.
- Foam should be left to cure, for approximately 1 hour before cutting expanded foam.
- After curing, excess foam coming out of the joint should be cut away. DO NOT press half-cured foam back into the joint as this destroys the foam structure.
- The exposed foam should be covered up or sealed with plaster, sealant, architrave or other material.
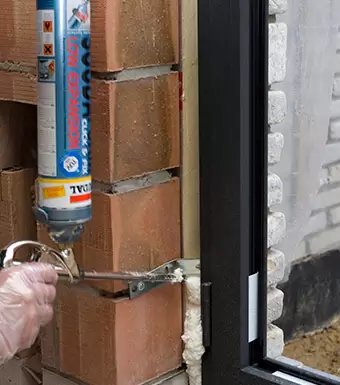
PU foam types
Single component (1K) PU foams cure through a reaction of the pre-polymer with moisture. After full cure (60-90min for 30mm bead), they ensure a strong bond and excellent insulation values. In order to optimize the curing and to ensure a good foam cell structure, substrates need to be moistened before the application.
Two component (2K) PU foams cure much faster as the pre-polymer reacts with a catalyst which is released when the can is activated. These foams are especially used for closed cavity applications where no moisture is available. The foam will cure within 5 minutes and needs to be applied at one shot and cannot be stored once opened. The density of 2K foams is high (35kg/m²) compared to 1K foams (20-25kg/m2).
Gun Foams vs. Straw Foams
Gun foams are mostly used by professionals and frequent users. Gun foams require a special foam gun that has a special function in frothing the foam as it is extruded and has following properties:
- High yield, low density
- Low expansion
- Convenient application – less wastage
- Requires Gun and Foam Cleaner and proper cleaning of gun
Straw foams are used mostly by DIY (Do-It-Yourself) and occasional users. Straw foams are easy-to-use and do not require any special tools and has following properties:
- Medium yield, medium density
- Triple expansion
- Quasi one-shot application: straw must be replaced
Performance Measures
Yield versus density
The performance of PU foam can be measured in several parameters; some being easily visually judged; like yield and cell structure, and others not so apparent; such as density or dimensional stability.
It is important to note that some of these parameters are inter-related. The most obvious and important relationship is that between yield and density: for the same volume of material, higher yield (in running meters) means lower density, and vice versa.
As a PU foam product increases in density, it brings about benefits such as better dimensional stability and mechanical strength, but at the same time, it has an inverse relationship on yield and curing speed.
Therefore, a good PU foam is one that balances these different properties into a product with the best efficiency in performance – high yield, but with enough density to ensure good stability and structure.
Foam Structure
The structure of the foam refers to the foam cells – these cells can range from very fine to very coarse. The finer the foam structure the higher the quality and stability of the foam, and the better the insulation properties.
On the other and, coarse cell structures and evidence of large holes or voids in the foam structure are indications of bad foam quality – reducing the effectiveness of the foam.
In extreme cases, very bad foam structure may lead to foam collapse – a phenomenon where the foam has a hollow foam skin with no cell structure inside.
fig. 4
Top picture show best cell structure – bottom picture show worst cell structure
Dimensional Stability
Dimensional stability is the stability of the foam after it has completely cured. A foam that has poor dimensional stability will create pressure to the joint, caused by expanding or shrinking foam after the foam is cured, usually a matter of days or weeks. This can cause deformation in the doors and windows, creating problems like misalignment of door frames, making it difficult to close the door.
In the case of one-component foams, a product with good dimensional stability will have less than 5% of expansion. Anything less than 10% will still be considered acceptable, while anything more than 10% will be unacceptable.
Sagging of foam –PU foam needs stability to stay in the joint (see left foam)
Expansion
The expansion of foam is the increase in volume of the extruded foam immediately after application. This should not be mistaken for curing pressure or dimensional stability.
Expansion of foam does not cause deformation of joints – expansion of foam can be welcomed in applications requiring the filling of cavities.
Expansion of foam can be further categorized into two types: controlled expansion and uncontrolled expansion, also known as high post-expansion.
- Foams with controlled expansion (gun type – low expansion foams) have a smaller rate of expansion (50-60%) and do not require a long time to reach its final size.
- Foam with high post-expansion (straw type – triple expansion foams) exhibits a sustained increase in volume (150-200%) over a longer period of time, and reaches a larger size (higher rate of expansion) as a final result.
Shear Strength and Mechanical Strength
Shear strength is the strength of both the adhesive strength (strength of bonding between substrate and foam) and cohesive strength (strength within the foam itself) of the foam. Shear strength resists the forces when two surfaces bonded by foam are pulled apart. The higher the density of the foam, the higher is its shear strength. Higher shear strength means better mechanical strength, and hence a better foam.
Influencing factors for foam quality
PU foams, as chemical products, are reliant on several factors for their structure, yield, and other properties. A knowledge of these factors could maximise the efficiency of PU foam products by an experienced user.
Temperature
Most PU foams perform best in temperatures between 20 to 25 degrees Celsius. Low temperatures may cause sagging, while high temperatures may affect the dimensional stability.
For temperature, there are two factors at play – firstly the temperature of the environment; and secondly the temperature of the can.
It is recommended to keep the can at room temperature (around 20 degrees) for at least 4 hours before using. During hot season the PU foam can could be cooled down by putting it in a bucket of cold water for some time.
Humidity
PU foam cures by drawing moisture from the air in its curing process. As a result, humidity is a very imporant factor. A few tips for optimizing the quality of foam:
Spraying the foam with water when air humidity is low quickens the curing reaction and improves the cell structure of the foam.
Spraying the surface of the joint where foam will be sprayed (e.g. door, window ) before applying the foam promotes adhesion and ensures faster curing of the foam.
Gun (for Gun foams)
An important aspect of achieving good quality of gun foams is the gun itself. Different guns can achieve very different results for the same can of PU foam.
PU foam guns are an important tool for the delivery of PU foam. It acts as a “frothing agent” so that the foam, upon exiting the gun barrel, is “fluffy”. This allows it to be in an optimal state for expansion and to achieve a good foam and cell structure.
However, the quality of the PU foam gun and its components can make a very large difference. A good gun can deliver as much as 30% more yield for the same can of foam than a poor gun. Besides yield, guns can also affect the density, foam cell structure, expansion, and mechanical strength.
As long as guns are properly cleaned and maintained, it is always a good idea to use a better gun for foaming applications to ensure optimal foam performance. In addition, high quality guns have a longer service life – poor quality guns are prone to blockages, jams and other problems even if properly cleaned. As a result, using a high quality gun makes good economic sense, despite the higher cost of the gun.
Post A Comment