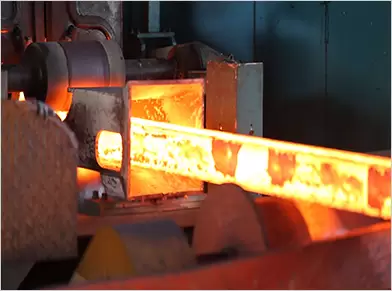
- Hot extrusion is the most commonly used method of extrusion for metals.
- In hot extrusion a very heated billet is forced to flow through the shaped dye orifice under very high temperature and pressure. The shape of the dye defines the shape of the finished product. It is a complicated process and requires careful attention and control during manufacturing. Due to the high heat the life of the dye also gets affected and reduced.
- The disadvantage is that the metal can get oxidized under very high temperature and cause friction in the metal flow. Hence the dye should be well lubricated. This does not happen in cold extrusion.
- Hot Extrusion results in a product with homogeneous properties, increased strength and improved quality of the finished product. The process also involves energy and material savings.
Post A Comment