Spontaneous Breakages
Most of us have come across a situation where a tempered (toughened) glass has broken without a provocation or any apparent reason. Non-tempered glasses do also break and sometimes, without any visible reason. Any non-tempered glass will normally break as a single crack or multiple cracks, which develop or propagate from origin either spontaneously or gently. Spontaneous breakage in tempered glass is however much more dramatic, as the whole pane of tempered glass breaks with a loud noise and high visibility as it breaks into thousands of small pieces.
Post your Requirement
Most of the times, a tempered glass will disintegrate and fall out of the fixing, but the cause of breakage can be assessed with reasonable fairness, if it stays in fixing. Breakages due to impact or wind loading are less likely to stay in frame. A tempered laminated glass will almost always stay in place after breakage and makes it easier to identify and analyze the cause. By simply looking at the point of origin of breakage and its pattern, the cause can be identified in most cases.
Causes of breakages
There can be several causes or reasons for spontaneous breakages in tempered glass like impact load, poor glazing, glass to glass contact, glass to metal contact, very hard setting blocks etc. Any of these can result in creating a concentrated point load on the edge or corner of the glass. In such cases, the point of origin of breakage will generally give a clue.
Improper or uneven tempering can also cause a post installation breakage. This will happen only if the stress differences on the same pane of glass are very large and this can be easily identified from such breakage. The breakage pattern will be highly non-uniform with some large islands of non-fragmented glass, enclosed or surrounded by much smaller fragments.
Read also : What is Tempered Glass?
Breakage due to uneven tempering
Breakages due to Nickel Sulfide
While the causes mentioned in previous section, can be attributed to errors in designing, manufacturing or glazing, there is one cause, which cannot be attributed to any of these and cannot be fully eliminated or fully addresses. It is the breakages caused by Nickel sulfide inclusions. Looking at the broken glass will give an initial impression of glass being hit by a sharp object and the point of origin of breakage will be obvious. On closer examination, at the origin, there will be at least two fragments in the shape of wings of the butterfly. (see image-2) This is often called ‘butterfly pattern’ or ‘double D Pattern’. The origin of breakage is generally away from the edge of glass.
The phenomenon was first acknowledged in 1940 but the first documentation happened in 1961. Since then, there has been extensive research by many companies, institutes and scientists to identify, prevent and resolve the issue. Standards have evolved and many extensive publications have been made on the subject. There have been a number of case studies on manufacturing processes and on glazed building as well. The entire community of designers, specifiers, manufacturers, fabricators and glaziers etc are now broadly aware of the problem. The industry has come a long way and has made rapid strides in addressing the problem, but the problem still remains to be fully resolved.
To understand this phenomenon of spontaneous breakages due to nickel sulfide, we need to briefly understand the manufacturing process of float glass and its heat treatment namely tempering, heat strengthening and heat soak testing.
Annealed Glass
Float Glass or annealed flat glass is the most basic form of glass. This is made of five basic ingredients namely silica sand, soda ash, dolomite, limestone, and salt cake. These are heated in huge furnaces to 1400-1500 degrees C, and then made to float out on a pool of molten tin in controlled atmosphere. The large sheets are pulled onto a conveyor, and taken through an annealing tunnel called lehr, where it is cooled very slowly for an evenly controlled heat dissipation rate. If it is allowed to cool rapidly or in uneven manner, it will result into cracking while manufacturing or in service due to uneven stresses. The cooled glass is cut into large sheets, and then sent to other processing locations for finishing, such as cutting to size, strengthening, or insulating. A large glass furnace can easily produce from 500 to 800 tons of glass each day.
Heat Strengthened and Tempered Glass
Heat Strengthened and tempered glass are created through the same process. At a processing plant, large sheets of annealed glass are cut to the appropriate sizes and shapes. The edges are ground and any holes or cutouts required in the panels are created. It is then heated in a furnace to a temperature of 600-700 degrees C. This temperature is held until the glass softens slightly, at which time it is rapidly cooled through the use of air jets, a process called quenching. Quenching reduces the temperature of the surfaces of the glass quickly and significantly, but due to the low thermal conductivity of glass, the core of the panel remains at a much higher temperature. As this core cools, it induces compression in the already-cooled outer layers, and a balancing tension force is formed in the core of the panel. (See diagrams –3a and 3b)
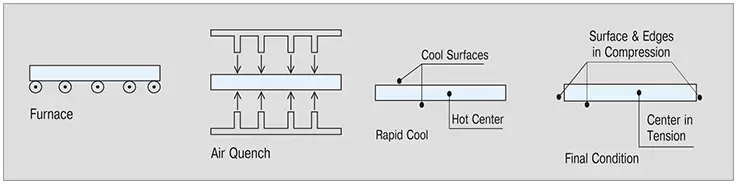
Process of Tempering
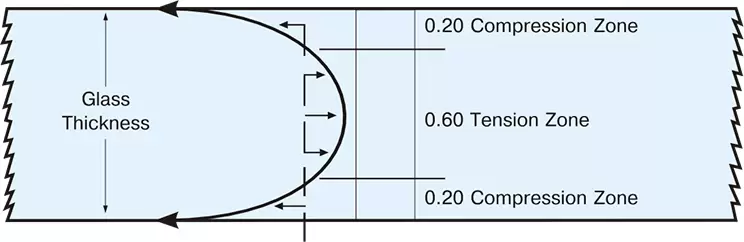
Stress Distribution in Tempered glass
The difference between heat-strengthened and tempered glass is the speed at which they are cooled, which results in different surface compressions and therefore different overall glass strengths and properties, which are compared as under:
Properties | Tempered Glass | Heat strengthened glass | Annealed Glass |
---|---|---|---|
Thermal stress | Upto 2500C | Upto 1300C | Upto 500C |
Strength | 4 times of annealed | 2 times of annealed | Not strong |
Bending strength | 120 – 200 N/mm2 | 60 – 100 N/mm2 | 40 N/mm2 |
design stress | 50 Mpa | 27 Mpa | 17 Mpa |
Surface compression | >10,000 psi (69 Mpa) | 3,500-7,500psi (24-52 Mpa) | Upto 2800 psi (19 MPa) |
Safety | Approved as safety glazing for most applications | Not approved as safety glazing | Not approved as safety glazing |
Site alterations | Not possible | Not possible | Possible |
Flatness | Slight bow and corrugation | Bow and corrugation lower than tempered glass | Very flat |
Optics | Reasonably good | Good. Comparatively better than tempered glass | Very good |
Lamination | Min 1.52 PVB | Min 0.76 PVB | Min 0.38mm PVB |
NiS breakage | Prone | Extremely rare possibility | Non existent |
Heat Soaking | Recommended | Not necessary | Not required |
NiS in the Glass Production Process
Some microscopic imperfections, known as inclusions, are inherent in the glass production process. Inclusions are microscopic particles that are incorporated into the structure of the glass in the initial melting process of silica sand and other ingredients. There are approximately 50 different types of dirt or other inclusions recognized, but almost all of them are completely harmless. Nickel sulfide is the only exception, and it is a problem in tempered glass only.
There is a reasonable consensus in the industry as to how NiS is formed, from the compounds that are initially introduced into the glass. Assuming that the nickel enters in the form of a nickel-alloy metal (like stainless steel), which is the most commonly accepted explanation for its origin, nickel sulfide forms in a three-step process. First, the nickel separates from the other materials in the alloy, then it bonds with sulfur in the high heat of the melting furnace, and finally is trapped in the glass as the glass cools to its sheet form. Major strides have been made in reducing the contamination of raw materials, and great care is taken to avoid the contact between the raw materials and any nickel-containing alloys but it is practically impossible to prevent some microscopic quantities finding the way into the melt, from other sources of Nickel.
Nickel sulfide, like many compounds, exists in different phases at different temperatures. There are two specific phases of NiS, known as the alpha-phase and the beta-phase. This would have no effect on glass whatsoever were it not for the fact that when the NiS changes from alpha-phase to beta-phase, it increases in volume by 2-4 per cent. At temperatures below 3800C, nickel sulfide is stable in the beta-phase form. Above this temperature, it is stable in the alpha-phase. Therefore, when glass is produced in the furnace, it is overwhelmingly likely that any NiS inclusions will be in the alpha-phase. In typical annealed glass, the slow cooling process provided by the annealing lehr, allows the NiS, ample time to transform to its beta-phase as the glass cools.
In the fast cooling process used in tempered glass, and also heat strengthened glass, there is insufficient time to complete the phase transition of NiS from alpha to beta. The inclusions therefore are trapped in the glass in their high temperature alpha-phase.
Once the glass cools past the phase change temperature, the NiS inclusion seeks to re-enter its lower energy beta-phase. For “trapped” inclusions, this process takes anywhere from months to years. This expansion creates localized tensile stresses that are estimated to be as high as 125,000 psi (860 MPa) at the glass-NiS Interaction surface. The magnitude of this stress drops off sharply away from the face of the inclusion, but is sufficient at the face to cause micro-cracking. (See image 4 and 5).
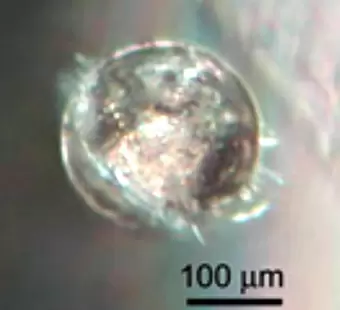
NiS Particle causing Micro Cracks
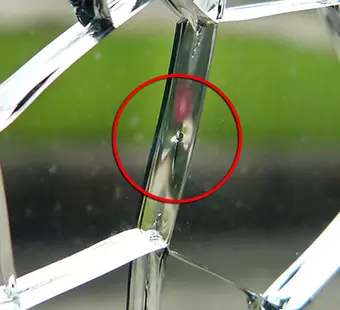
NiS Particle photographed after spontaneous breakage
In compression zones, even this large of a stress is not a concern due to its extreme localization. However, in the core tension zone of the glass, these micro-cracks are propagated by stress concentrations at the tip of the crack until the structure of the glass is undermined completely and the tempered glass undergoes its characteristic shattering, which causes the seemingly spontaneous failure.
For simplified explanation, one can imagine tempered glass as akin to an inflated balloon, which can take substantial loads but when pricked or triggered by a sharp object, it will burst very easily. If there is a NiS particle sitting in the tensile zone or very close to it, the phase change from alpha to beta, can act as a trigger and cause the spontaneous breakage. Tempered glass with higher stresses, will have higher probability of NiS breakage as compared to tempered glass with lower stresses, just as a more pressurized balloon will need lesser provocative force to trigger its bursting. It has been observed that the incidences of NiS breakages are more in thicker tempered glasses (8mm-19mm) as compared to thinner glasses (4mm-6mm).
Heat strengthened glass has substantially lower stresses than tempered glass and therefore have very little possibility of NiS breakages.
Critical vs. Sub-Critical Inclusions
Research has created a theoretical equation that predicts the smallest diameter of a NiS inclusion that would cause failure as 50 microns (0.05mm) in diameter. Inclusions larger than this are typically referred to as “critical” inclusions, whereas smaller inclusions are classified as “sub-critical” inclusions. The relationship between stress and diameter of NiS inclusion has been scientifically proven and field studies have also examples of such small inclusions causing the spontaneous breakages.
It is important to note that sub-critical inclusions of size substantially lower than 0.05mm (say 0.02mm) are generally not capable of creating enough localized tensile stresses, to be able to break the glass, but these can cause a failure if the glass is placed under additional tensile stress due to bending or thermal loading. It has been shown that when glass undergoes deflections that are in excess of 75 per cent of the panel thickness, the stresses in the glass due to lateral loads change from a bending stress profile to a membrane stress profile. Under this condition, lateral loads may increase the tensile stresses at the center of the glass.
Breakage Frequency and Timeline
NiS breakage occurrences are not very significant if we consider the total volume of tempered glass produced globally or nationally, and the volume of glass broken due to NiS. There are many buildings with no report of NiS breakages. There are quite a few which have experienced an occasional failure, but there are some examples, which have repeated failures.
It has not been possible to put exact numbers on frequency and timeline since the results of various studies are all different in units. One study puts the number of NiS occurring as 1 in 500 glass panes. Another study by a prominent Indian float manufacturer puts the no. as 1 critical occurrence in 13 tons of glass. Many other studies have come out with different numbers and though the numbers do not match, it seems clear that failures due to NiS inclusions are incredibly rare. Buildings that have seen multiple instances of NiS failures often have huge expanses of glass, which automatically increases the odds of such a failure occurring. It is also possible for a particularly bad batch of float glass to be produced, which would have a higher failure rate.
Another aspect of nickel sulfide failure is the fact that these failures rarely occur upon installation or even within the first few months following installation. Even so, the overwhelming trend is that most panels break in the first 2 to 7 years, after which the number of breakages tapers off with what is commonly considered a logarithmic decay.
Preventative Measures
The industry is pursuing several courses of action in order to reduce the risks and costs associated with nickel sulfide in tempered glass. For the purposes of comparing various preventative or corrective methods, three criterions were selected which seem to be a fair evaluation of the effectiveness of a solution. In order to be a successful solution, the method must be cost-effective to implement, eliminate the costs of replacement of panels upon breakage, and prevent any injury to bystanders in a failure. So far, no solution has adequately fulfilled all three criteria, and thus the industry is still searching. However, a summary of preventative measures already in use or development in the industry is discussed here.
Controlling NiS in Annealed Glass
It might seem the simplest solution to nip the problem at its origin by ensuring that there is no nickel or its alloys entering the glass-melting furnace. Responsible float manufacturers are supposed to take every precaution to control this but it is very difficult to prevent it altogether and in spite of best efforts, small amounts of nickel will find its way through inclusions in raw materials itself or their handling/ storage equipment’s etc. There is a need for float manufacturers to further strengthen the quality procedures to include necessary steps for its prevention and to subject their quality procedures to internal and external quality audits.
Heat Soak Testing
Tempered glasses can be heat soaked by heating the glass panels for a third time to a temperature below the phase change temperature of NiS and maintaining it or soaking it at that elevated temperature for a set time. Maintaining an elevated temperature facilitates faster conversion of any particle of NiS, if present, from alpha-phase to beta-phase, and therefore the idea is that any panel, which has a possibility of failure from NiS, should fail in the HST oven rather than on the building. The process was introduced in 1982 and the first standard that evolved was DIN 18516. The most common standard, currently being followed is EN 14179. This standard requires glass to be heated to 290±10 C and held at this temperature for 2 hours, which is a shorter duration than 8 hours for DIN 18516. The reduction in time was based on recommendations from research, which indicated that less than 1 break in 10,000 panes of glass was expected to occur after 2 hours.
There are costs associated to HST which are the processing costs, cost of glass breakages due to NiS in HST oven, and damage by broken glass to the neighboring panels in HST oven, potentially even causing them to break as well and propagating the problem.
Another issue is that the secondary heating of tempered glass relaxes surface compression slightly without a corresponding decrease in core tension, which reduces the strength of the glass, though marginally. This was more evident in the 8 hours soaking specified in DIN than in the 2 hours soaking as per EN. The designers should keep a small safety margin to account for the same.
In spite of all the issues with the process, it is still the only method the industry has, to eliminate a large portion of nickel sulfide inclusions in batches that are compatible with large-volume production. The success rate of HST is hard to define because of the difficulty of accurate data collection on resulting nickel sulfide failures, which are very rare occurrences. But it can be safely said that appropriately done HST, would eliminate 95 to 98.5 per cent of such glasses as could have caused a spontaneous breakage post installation.
Smart specification and selection
The most logical solution to the problem is by avoiding the use of tempered glass where there are other options like
- Use heat-strengthened glass instead of tempered glass where technically feasible.
- Heat strengthened laminated glass is the best option for most applications, except for point fixed glazing
- In applications, where tempered glass cannot be avoided due to load considerations or code requirements, it is advised to get it HST.
- Alternately one should be prepared for such occurrences and for replacing NiS broken glasses.
- Annealed Laminated glass will have no occurrence of NiS breakage.
Other methods for detection
There are other methods such as laser-imaging and ultra-sound which are non destructive but these methods will need a scan of each panel of glass which will show up all inclusions and not only NiS and thereafter, it will separately need an assessment of each inclusion in each panel to decide which ones are fatal types of NiS and located in the risk zone. The exercise is prohibitively expensive and not feasible on production scales. A person must interpret the results of ultrasound and laser imaging, glass by glass and the margin of user error might be quite large when searching for such a small problem.
Conclusions
Spontaneous breakage due to NiS is not due to any manufacturing defect but is an inherent risk or problem associated with use of tempered glass. As of now, 100 per cent success in eliminating nickel sulfide from tempered glass cannot be guaranteed by any method. Therefore this is an issue which designers should be aware of, and take into account when deciding the use of tempered glass in their building and adopt smart specifications. Glass is a fragile material and no glass supplier can warranty breakages, as there can be numerous causes of breakages and NiS breakages is just one amongst many.
Post A Comment